Operating principle
Once the suspension fed into the centrifuge drum via feed pipe, solid phase of it of higher density will be settled down and attached to wall surface of the rotor drum under effect of centrifuge field. which will be screw pushed to drying area before it's discharged via slag outlet,the clarified Iiquid phase of it will be overflowed via the overflow port of the rotor drum,hence to realize solid and liquid separation.
LWF is explosion-proof type.
Main features
Components/parts including drum and screw etc that will be in contact with the feedstock are made of corrosion resistant stainless steel,duplex steel or C22 according to the working condition.
u High precision rotary drum(NC machining,high-precision balance),high separation factor, improved separation efficieney.
u Dual variable frequency common DC bus control, step-less velocity adjustment of drum and screw;
u A variety of lubrication methods: grease lubrication (standard),oil injection lubrication,oil and gas Iubrication.
u Fully automatic oil recharging device
u Surface of the spiral vane is sprayed with wear-resistant alloy or welding hard alloy.
u Different differential mechanism is equipped for different working conditions,i.e. cycloid pin, planet gear or hydraulic differential.
u Fully enclosed system satisfying specification of pharma production
u Multiple layers of protection including over-vibration protection,cover opening protection,motor overload protection,differential speed/torque control and switch, bearing temperature detection,screw pushing torque protection,static grounding protection and Iocking protection for maintenance
u N2 protection system and relevant ex-proof measures are equipped to satisfying ex-proof specification
u Can be core part of a waste water treatment system once combined with flocculant dosing system, screw pump, flow meter and other fittings
Personal form
Centrifuga casting of rotor drum
u The rotor drum is made by means of centrifugal casting and solution treatment,which means better stability
u Higher strength
u Can be made of various material including 304、316L、2205、C22、C276
Screw wear-resistance treatment
u Cemented carbide insert
Tungsten carbide alloy
Built-in structure
u Cemonted carbide coated surface
Tungsten carbide coated
Differential mechanism
u Cycloid pin wheel differential
u Pianetary gear differential
Larger torque output
Stable and reliable operation
u Hydraulic differential mechanism
Better Iow differential output
Differential stepless adjustable
Compact structure
Sealing performance
u Shaft seal design
ensuring effective separation between the working cavity and bearing cavity
u Flexible joint for slag discharge and transfer connection
Flexible joint or transfer connection for option of installation design
Liquid phase to be discharged by centripetal-pump
u Liquid phase will be discharged by centripetal pump,with liquid level programmable as per process requirements
u Good sealing performance of the whole system
Three-phase sparation
u Applicable for solid-Iiquid-liquid separation
u Heavier Iiquid to be discharged by centripetal pump (Liquid level adjustable)
u Lighter Iiquid to be overflowed via overflow port of the rotor drum (liquid level adjustable)
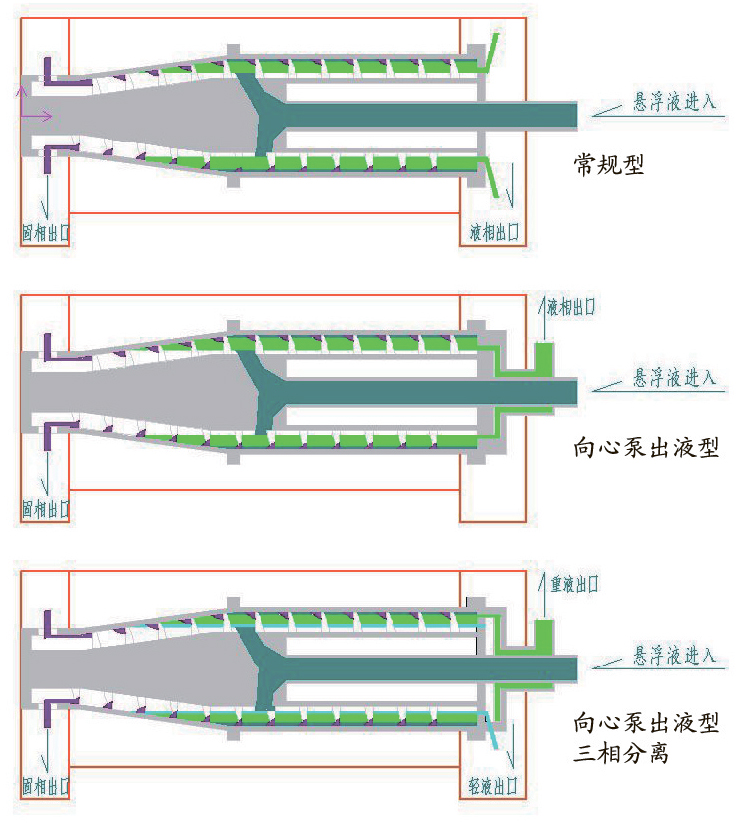
Technical parameter
u Please refer to the Table above for technical parameters for LWF.
u Ratio of length to diameter shown in above Table are generic parameter,which is subject to adjustment base on working conditions in order to achieve satisfying performance of separation.
Explosion-proof and sealing
u Sealing of the whole system
u Shaft seal design
u N2 protection system
u Slag discharge connection/joint
u Explosion proof and separation measures
(Refer to Application of Ex-proof Technology for detail)